Coalesces Oil & Water Separators
Tilted Plate Pack Oil & Water Separators
Coalesces Oil & Water Separators
Tilted Plate Pack Oil & Water Separators
Ecotech Africa’s Oil/Water Separators feature a unique design based on Stoke’s law that results in suspended solids settling at the bottom while oil rises to the top. This design promotes the easy and effective management of waste water. When we design our Oil/Water Separators, we take the following important factors into consideration:
Advantages of Ecotech Africa’s Oil/Water Separators:
Ecotech Africa recognises the need




General Overview
Oil & water separators are typically considered very simple devices.
However, several factors that could potentially affect safety, efficiency, and proper management must be given careful consideration prior to the installation or modification of any oil/water separators or separation systems:
Design Calculation to Achieve Optimal Segregation
To calculate the size of an empty vessel gravity separator, it is first necessary to calculate by the use of Stokes’s Law the rise velocity of the oil droplets. The size of the separator is then calculated by considering the path of a droplet entering at the bottom of one end of the separator and exiting from the other end of the separator. Sufficient volume (residence time or retention time) must be provided in the separator so that an oil droplet entering the separator at the bottom of the inlet end of the separator has time to rise to the surface before the water carrying the droplet exits the opposite end of the separator. We can confidently predict that the separator will meet the effluent standards necessary under the law.
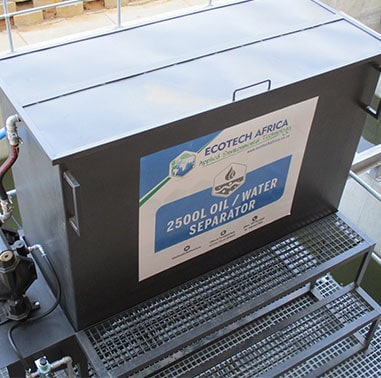
Flow Rate
In general, separators are sized by the flow rate verses the separation chamber’s effective surface area (or projected surface area in the case of a “coalescing” or parallel plate type separator). Therefore, the effectiveness of any oil water separator is affected by the flow rate. The slower the flow, the better the results.
Design Capacity
An oil water separator has upper limits to the amounts of oil and sludge that can effectively accumulate while it is in operation. If too much oil accumulates in the receiving and middle chambers, it may flow into the wastewater outlet chamber and end up being dis charged to the environment. Proper oil water separator design will allow for the removal and storage of accumulated oil and sludge from the separator to ensure that the accumulated products do not affect the operation of the separator.
Emulsifying Agents
Detergents and soaps designed to remove oily grime from equipment, vehicles, or other components can adversely affect the operation of a gravity oil water separator. These types of surfactants, or “emulsifying”agents, are specifically formulated to increase the dispersal of oil into water, which why they are such good cleaners. When these soapy wastewaters enter an oil water separator, it takes significantly longer for the oil to separate, if it can, from the water. Excessive use of detergent s can render an oil water separator in efficient by completely emulsifying oils into the wastewater stream and allowing them to pass through the system. Low-emulsifying soaps are available that allow oil separation to occur more quickly after the soapy water enters the oil water separator.
Maintenance Practices
The ability of oil water separators to function properly depends upon the timely performance of required service and maintenance. Oil/water separators must be monitored and maintained by competent personnel who understand how the systems operate. Oil/water separators should be given the same close attention given to any other important piece of equipment. The operators,users,and maintainers of the oil/water separator must clarify who will be responsible for monitoring, inspecting,maintaining, and servicing the system.
Frequent inspections should be made of the system and all associated piping, valves, etc. to prevent operational and mechanical failures or inefficiencies. Sludge and oil need to be periodically removed from the oil/water separator to keep it operating properly. Additionally, leaks from oil/water separators can result in environmental pollution, which can trigger costly investigative studies and cleanups. Rigorous implementation of an OWS inspection and maintenance plan can prevent discharges from the oil/water separator that may contaminate the environment
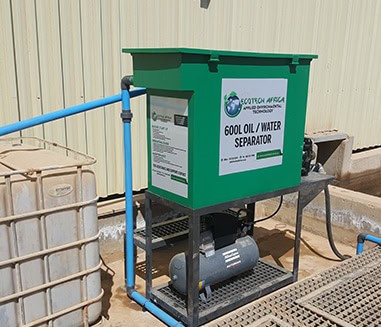

Suitability of Oil Water Separation System to Process
An oil/water separator designed and installed to meet a past process requirement may no longer be suitable when process requirements change, and/or the original maintenance plan is no longer followed. A oil/water separator that is put to a use for which it was not originally designed may be damaged or may not function properly, and could become an environmental liability. For example, an oil/water separator designed to receive the wastewater discharge from a small engine wash rack will not be able to properly treat larger wastewater volume from washing the exterior of locomotives. Process changes can also result in changes to the physical/chemical makeup of the wastewater being treated by an oil/water separator.
Finally, process changes may also necessitate the modification of storm water and wastewater drainage systems. Such systems should remain separate from each other because excessive drainage of storm water to an oil/water separator could significantly impair its operation and efficiency.
Contaminants Contained in the Wastewater System
Metallic particles in the wastewater will settle into the sludge at the bottom of the oil/water separator. Solvents or fuel compounds may also be entrained in the oil/water separators’ sludge. This sludge could require management under the Waste Act as a hazardous waste if it exhibits certain toxicity characteristics. Therefore, it is important to prohibit the discharge of certain types of potential contaminants into an oil/water separator, and to regularly analyse sludge samples to determine toxicity prior to disposal. To reduce the accumulation of sludge, floors should be dry-swept before washing. General improvements in spill/drip control and containment of hazardous materials and oils will also reduce the amount of contamination in oil/water separator discharges.
Latest & Current Projects
Stay up to date with all our new Projects - Follow us on Social Media
MAKE USE OF OUR EXPERTIES
Get your no obligation free quote today!